The motion accuracy of stepping servo motors is related to the following factors:
(1) Step angle:
The step angle of the stepper motor determines the amount of rotation for each step.
Usually, the step angle of a stepper motor is 1.8 degrees or 0.9 degrees.
Smaller step angles provide higher resolution and more precise position control.
(2) Drive mode:
The stepper motor can be driven by full step or micro step.
Full stepper drives apply current directly to the motor phases, causing them to move at fixed step angles.
Microstepping drives, on the other hand, achieve smoother motion by applying different currents between the two phases, which improves motion precision.
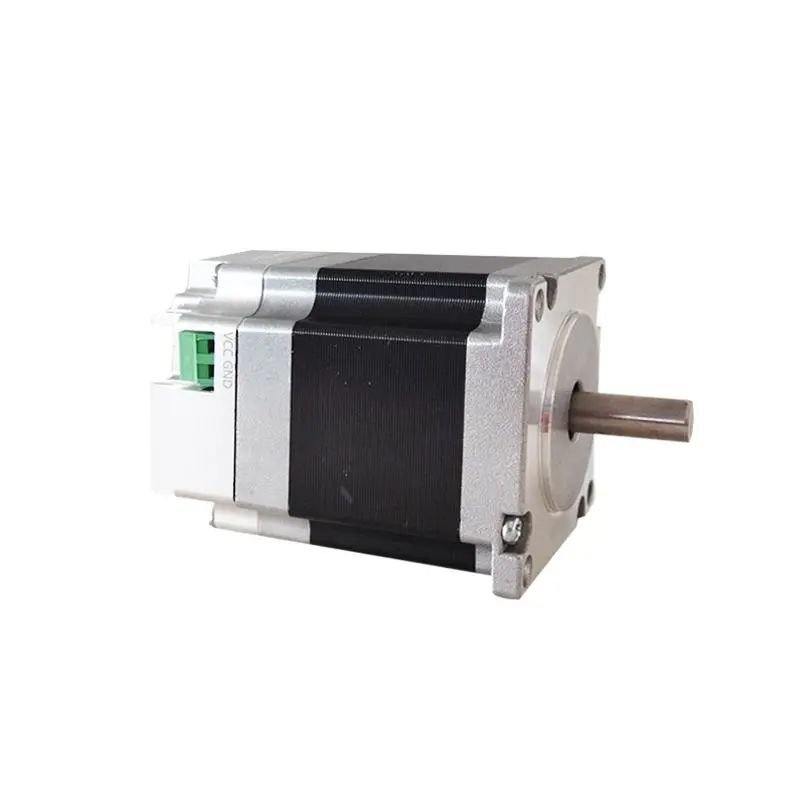
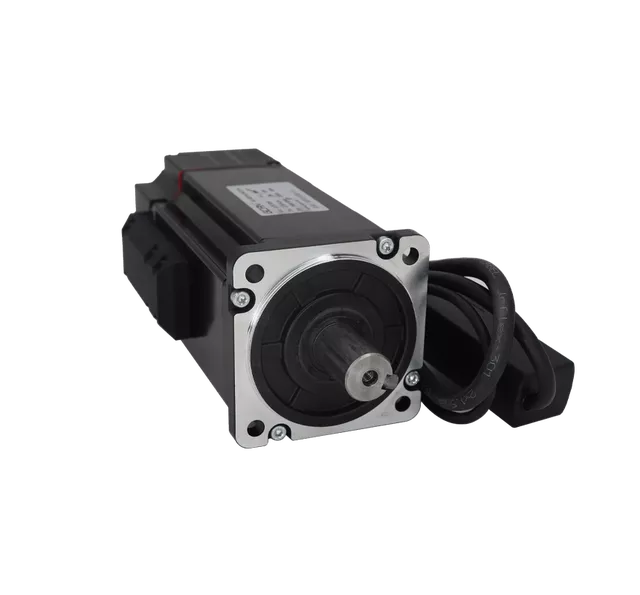
(3) Closed-loop control:
The stepping servo motor combines the characteristics of the stepping motor and the servo system, and can realize closed-loop control.
By using encoders or other position feedback devices, the position of the motor can be monitored and corrected in real time, thereby improving motion accuracy.
(4) Driver performance:
The driver of the stepping servo motor also plays an important role in the motion accuracy.
The performance of the driver includes output current, number of subdivision steps, current control method, etc.
Higher output current and more subdivision steps can provide more precise position control and smooth motion.
(5) Load and mechanical transmission system:
Factors such as the rigidity, accuracy and return error of the load and mechanical transmission system will also affect the motion accuracy of the stepping servo motor.
Higher loads and poor mechanical transmissions can cause motion distortion or positional deviations.
Looking for a CAN Fiber Optic Gateway for your next project ? Click to learn more!