Programmable Logic Controllers (PLCs) are integral to industrial automation and industrial process control. They manage various actuators, analog, and digital sensors, and communicate complex interfaces in changing protocols. Other than control functions, PLCs execute data conversion and signal processing.
PLCs have a variety of applications and uses, including process automation plants (e.g. mining, oil & gas), glass industry, paper industry, cement manufacturing, and in boilers – thermal power plants. They are used in transportation systems like conveyor belt systems. They are also used in wind turbine operation to help make wind turbines more efficient and experience less downtime.
The basic difference between Programmable Logic Controllers (PLCs) and Programmable Automation Controllers (PACs) lies in the programming interface of the two, making them serve different functions. PACs are programmed using C or C++, therefore, have an open architecture and incorporate modular design. Whereas, PLCs have simple program execution.
PLCs usually have a simple program with limited memory and minimal input/output (I/O) points. But a PAC can monitor and control thousands of I/O points. PACs are more intricate, using C or C++. PLCs on the other hand, are programmed using ladder logic.
Programmable Automation Controllers (PAC) are used in industrial control systems for machinery in a wide range of industries, including those involved in critical infrastructure. There are some disadvantages to using PACs in industrial control systems:
They can be complex to program and maintain, especially for those who are not familiar with the specialized programming language that is used to program them. The cost of PAC for small applications is high. When a problem occurs, hold-up time is indefinite, usually long. There are limitations of working PACs under high temperature, vibration conditions. Some PACs turn on when power is restored and may cause an accident.
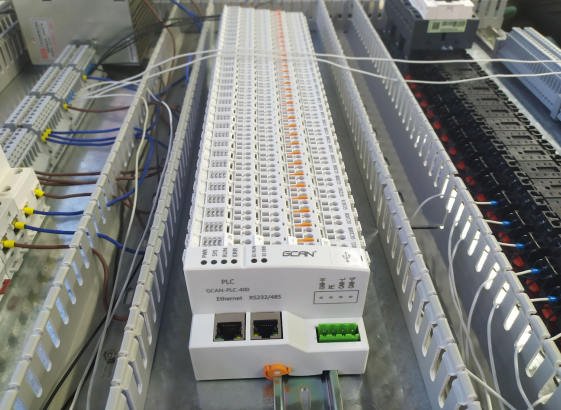
Looking for a PLC I/O Coupler? Click to learn more!