Single-turn and multi-turn encoders are devices used to measure the rotational position of servo motors, and the difference between them is mainly in the measurement range and accuracy.
Single-turn encoders: Single-turn encoders can only measure one turn (360 degrees) of rotational position.
It usually consists of a photoelectric sensor or a magnetic sensor, which can provide relatively basic position feedback information.
Single-turn encoders are suitable for applications that do not require high rotation angles, such as some simple positioning controls.
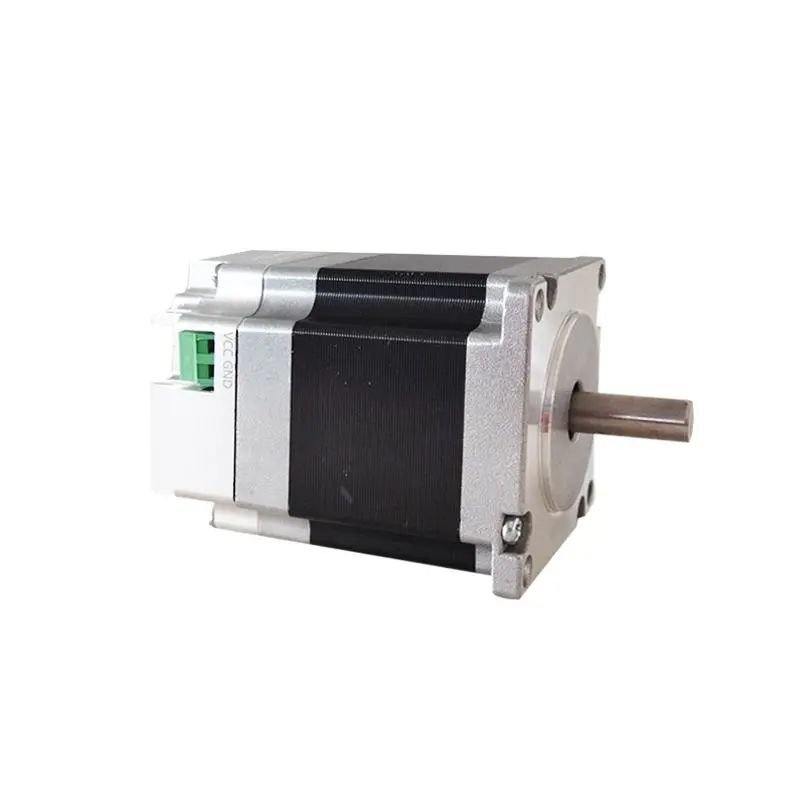
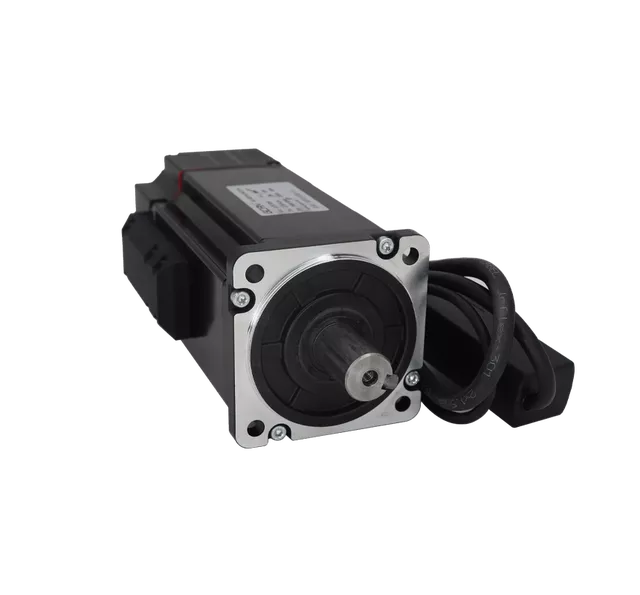
Multiturn Encoders: Multiturn encoders measure rotational position over multiple turns and typically include a single-turn portion and a multi-turn portion.
The multi-turn part can provide higher resolution and larger measurement range.
It usually uses technologies such as optical grating, magnetic or Hall effect, which can provide more precise position feedback information.
Multiturn encoders are suitable for applications that require high rotational angles, such as precision positioning and motion control.
Generally speaking, multi-turn encoders have higher resolution and larger measurement range than single-turn encoders, and can provide more accurate position feedback information.
However, multiturn encoders are also generally more complex and expensive, requiring higher technical requirements and capital investment.
Therefore, when selecting an encoder, it should be evaluated and selected according to the specific application needs and budget.
Looking for a CAN Fiber Optic Gateway for your next project ? Click to learn more!