As a PLC engineer or purchaser, it’s crucial to be aware of the potential physical hazards associated with PLCs. Understanding these risks and taking preventive measures can ensure the safety of both personnel and equipment. Let’s explore the different types of physical hazards PLCs face and how to avoid them.
1. Electrical Hazards
Electrical shock is a major concern when working with PLCs. Improperly touching live wires, coming into contact with conductive components, or working with poorly insulated parts can lead to serious injuries. Always follow proper electrical safety procedures, wear insulated gloves, and de-energize the system before performing any maintenance or troubleshooting tasks.
2. Mechanical Hazards
PLCs often consist of moving parts and machinery. It’s essential to be cautious during assembly, maintenance, and debugging processes to avoid getting fingers, hands, or other body parts caught, cut, pierced, or injured by rotating components, moving parts, or sharp edges. Always use appropriate personal protective equipment (PPE) and ensure proper machine guarding.
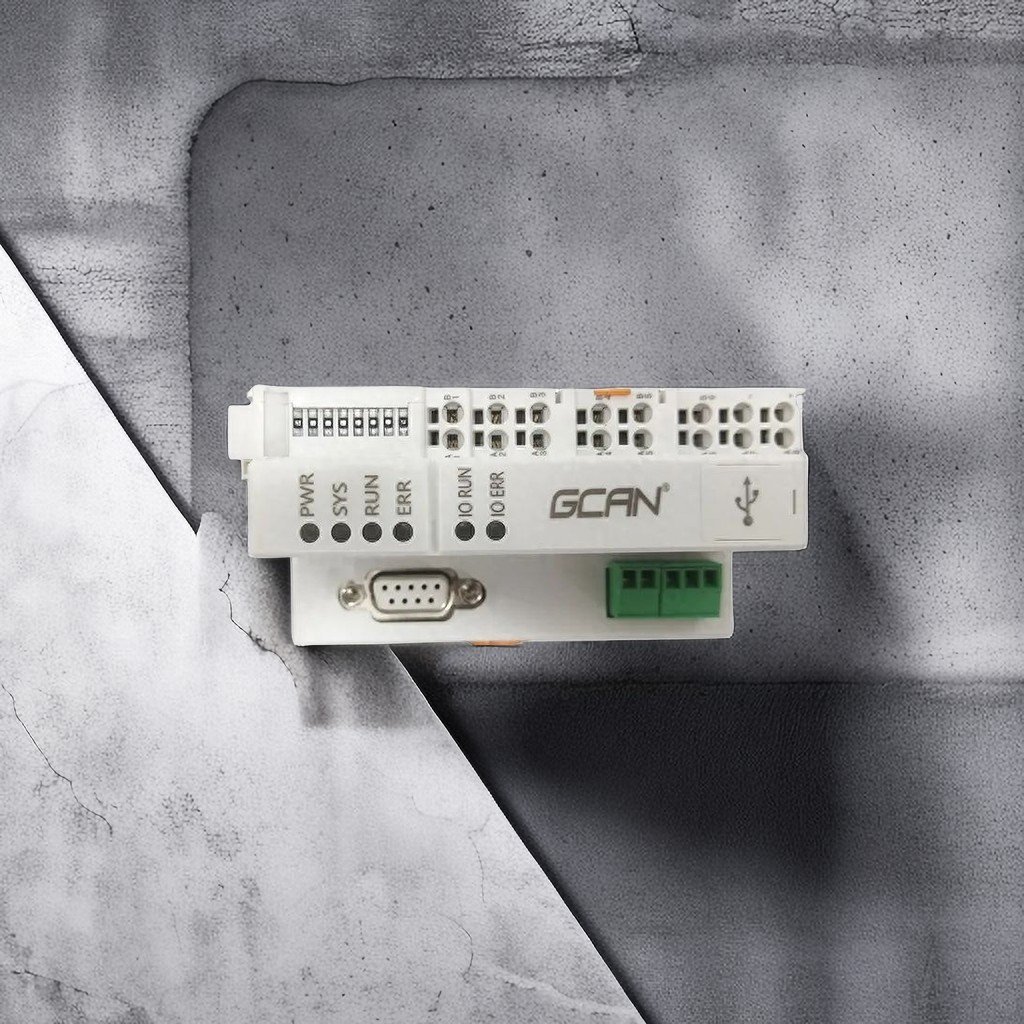
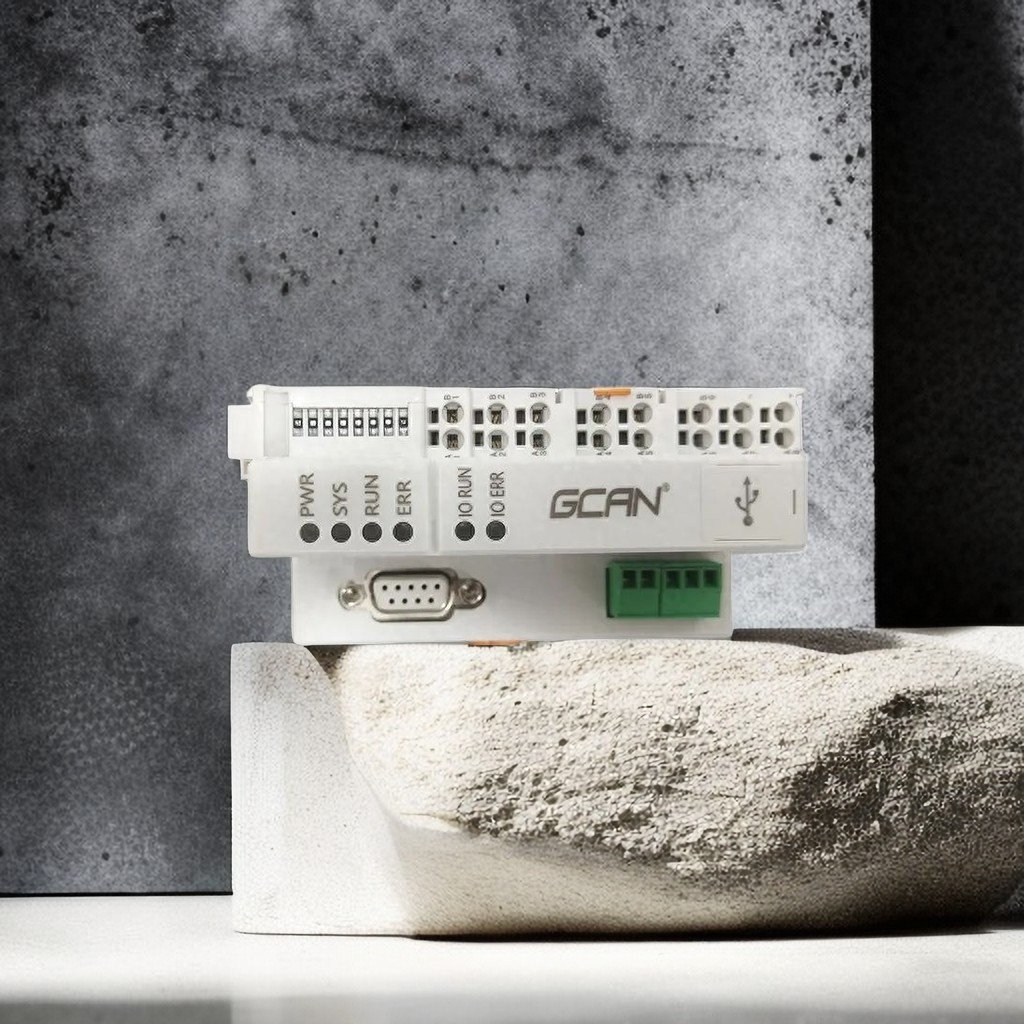
3. Thermal Hazards
PLCs are often used in conjunction with high-power electrical equipment, which can generate significant heat. Contact with hot surfaces or exposure to thermal radiation without proper protection or safe operating practices can result in burns. Always use heat-resistant gloves, keep a safe distance from hot surfaces, and ensure proper ventilation in the working area.
4. Chemical Hazards
In certain industrial environments, PLCs may be exposed to chemicals or corrosive substances. Improper handling or lack of appropriate protective equipment can lead to chemical burns or other chemical injuries. Familiarize yourself with the chemicals present in your work area, use proper ventilation, wear appropriate PPE, and follow safety guidelines and protocols.
5. Dust and Foreign Object Hazards
Industrial environments often have a significant amount of dust, particles, or other impurities. Accumulation of these particles inside or around PLCs can lead to short circuits, poor cooling, mechanical component failures, and even fire or explosion hazards. Regular cleaning, proper maintenance, and using dust-proof enclosures can help mitigate these risks.
Remember, safety should always be a top priority when working with PLCs. By being aware of the potential physical hazards and taking appropriate precautions, you can ensure a safe working environment for yourself and your colleagues.