(1) PLC can realize the comprehensive automatic control of the automatic loading system.
Through programming settings, automatic loading, unloading, positioning, transportation and other operations can be realized, reducing manual intervention and improving production efficiency and safety.
(2) PLC can accurately control each executive component in the automatic loading system, such as conveyor belt, mechanical arm, fixture, etc.
Through precise position control and speed adjustment, it can ensure accurate loading and unloading of materials, and improve the accuracy and consistency of loading.
(3) PLC can monitor the running status of the automatic loading system and issue a fault alarm in time.
This helps to quickly identify and resolve potential failure issues, reducing downtime and increasing productivity.
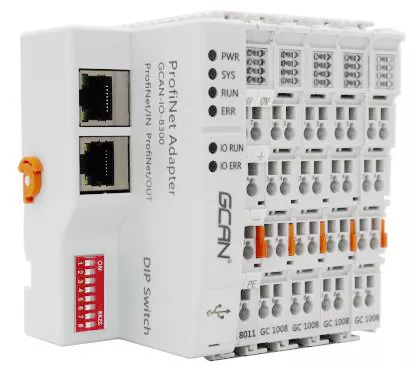

(4) PLC can record the operation data of the automatic loading system, such as loading quantity, loading time, fault information, etc.
These data can be used to analyze the performance and efficiency of the system, and make optimization and improvement to improve the efficiency and quality of loading.
(5) PLC has flexible programming capabilities and can be customized according to different loading requirements.
At the same time, the PLC system also has good scalability, and new sensors, actuators or functional modules can be easily added to meet changing loading requirements.
(6) The PLC system can realize the safety control of the automatic loading system, such as emergency shutdown, anti-collision protection and other functions.
By monitoring various safety sensors and equipment, PLC can ensure the safety during the loading process and avoid accidents.
Looking for a CAN Fiber Optic Gateway for your next project ? Click to learn more!