Testing and controlling a PLC is a multifaceted process designed to verify the functionality, performance, and stability of a PLC system. The following briefly explains the main steps and methods of testing and controlling PLC.
1. Check the power supply and input/output status of the PLC:
(1) Observe the status of the PLC’s power indication, error indication, and input/output indicator light to determine whether there is a power supply problem or input/output abnormality.
(2) Check whether the connection and communication between the PLC and external devices are normal by testing IO points, including operation buttons, emergency stop buttons, operation indicators, cylinders and their limit switches, etc.
2. Use the software diagnostic function:
(1) Many PLCs have built-in diagnostic programs that can detect hardware faults and output fault information. By accessing the PLC’s programming software or using specific diagnostic tools, diagnostic information can be read and analyzed to determine the specific cause of the failure.
(2) Compare whether the actual value matches the expected value to determine whether there is a fault point.
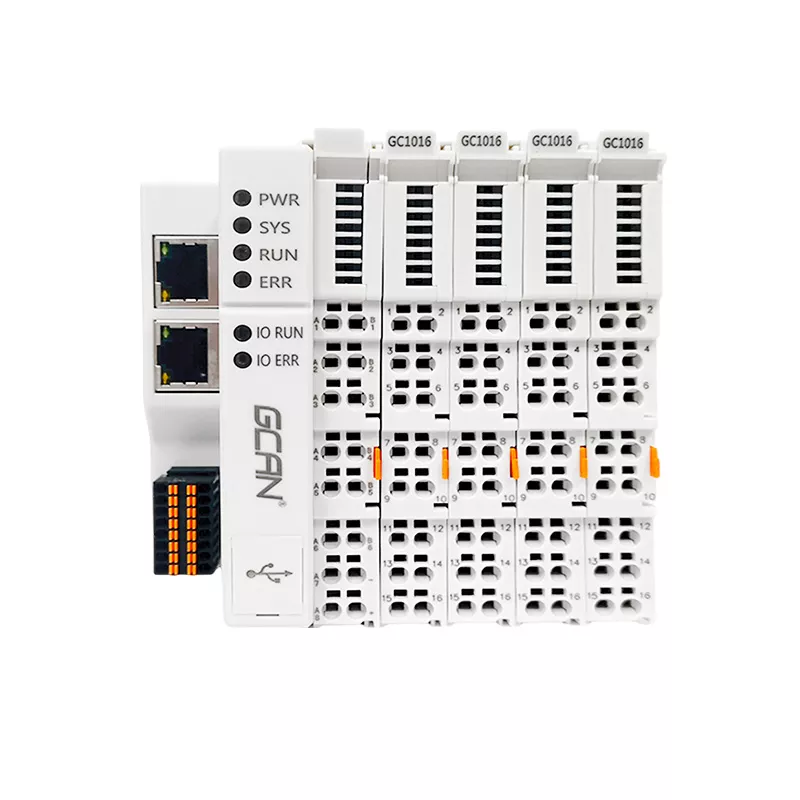
plc programmable logic controller china’s manufacturer low cost price

3. Check the logic program:
(1) Carefully check the PLC logic program to ensure that the logic conditions, timers, counters, etc. are set correctly and match the actual equipment operation.
(2) Check the fault detection and alarm logic in the logic program to determine whether there are potential fault points.
4. Communication status check:
(1) If the PLC communicates with other devices, such as human machine interface (HMI), sensors or actuators, please check the settings of the communication link and communication protocol.
(2) Use the network communication function of the PLC for fault diagnosis, use network analysis tools to monitor the communication process, and check whether the transmission of data packets is normal.
5. Hardware test:
(1) Use specialized diagnostic tools for fault detection, such as logic analyzers, oscilloscopes and other hardware test equipment.
(2) For large systems, a test table should be established, that is, marked after testing. If wiring errors are discovered during the construction process, they need to be dealt with immediately.
6. Check the mechanical structure and motor load:
(1) Check whether the mechanical structure is fastened, etc., and whether the motor load is properly protected to avoid accidents.
7. Debugging manual mode/semi-automatic mode and related logical relationships:
(1) Debug the automatic mode according to the production process to ensure that the PLC can work normally in different modes.
8. Check log files and alarm information:
(1) PLC systems usually record log files and alarm information, which can be used to record fault events. By viewing these files, you can determine when a failure occurred, its type, and its location.
9. Hardware reset:
(1) In some cases, the hardware reset method can be used to solve some temporary problems.
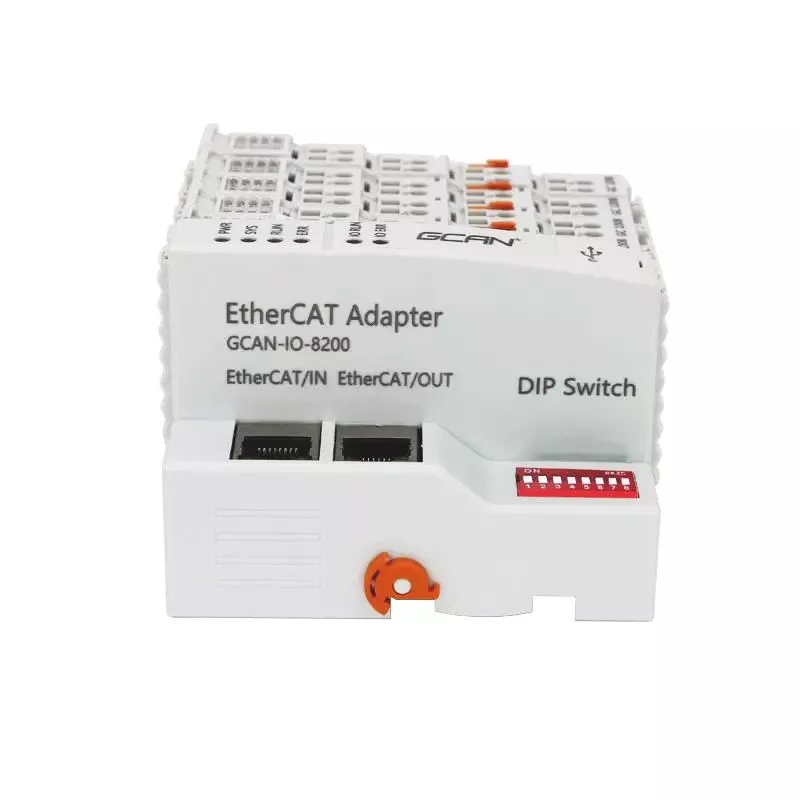
If you need a PLC that supports codesys programming, you are welcome to contact us at 86 136 4400 1762 at any time.