What are the causes of CAN data transmission errors?
CAN data transmission errors can be caused by many reasons, here are some common reasons:
(1) Hardware failure: Hardware problems, such as transceivers, connectors, or other components of the CAN network that are not working properly, may introduce “framing errors.” In addition, problems such as cable breakage, loose connectors or corrosion may cause CAN bus communication interruption or data transmission errors.
(2) Electrical problems: Power fluctuations or other electrical problems may affect the quality of the CAN signal and cause “frame errors.” For example, the baud rate does not match or the node is not initialized, which may also result in no ACK (response) signal.
(3) Environmental issues: Factors such as electromagnetic interference, voltage peaks or radioactive interference in the industrial environment may cause CAN bus communication errors. If the noise level in the external environment is higher than the tolerance level of the CAN bus, this noise may also be mistaken for signals, resulting in signal loss.

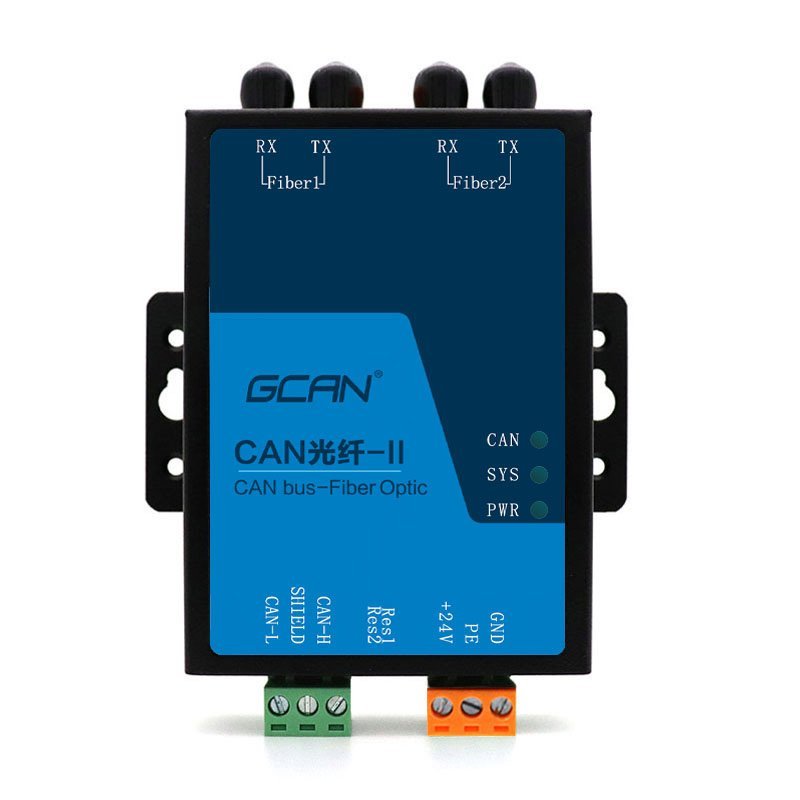
(4) Data conflict: In a CAN network with multiple nodes, if two or more nodes try to transmit at the same time, it may cause a collision and generate a “frame error”. This kind of data conflict is usually caused by improper implementation of the arbitration mechanism in the CAN protocol or node synchronization issues.
(5) Software problem: The communication protocols between control units may not match, resulting in signal loss. In addition, software issues such as programming errors, configuration issues, parameter errors, or hardware errors can also cause signal loss or transmission errors.
(6) Terminal resistor problem: A 120-ohm terminal resistor should be connected to both ends of the CAN bus. If the terminal resistor is damaged or not connected, it will cause signal interference and communication errors.
For the above possible causes, debugging and troubleshooting work may involve using specialized CAN debugging tools to monitor bus activity, check hardware configuration and electrical characteristics, and analyze and adjust software settings and parameters. These efforts are designed to ensure that the hardware and software of the CAN network comply with specifications and can transmit data stably and reliably under various environmental conditions.
If you need a CAN bus debugging tool to detect CAN data transmission errors, you can contact us at any time 0086 136 4400 1762.