Le servo pas à pas est un moteur pas à pas intégré à un encodeurqui peut renvoyer des informations sur la position, le couple et la vitesse du mouvement du moteur, et d'autres éléments sont fondamentalement les mêmes que les moteurs pas à pas ordinaires.
Un moteur pas à pas est un moteur qui convertit des signaux d'impulsion électriques en mouvement mécanique, et son principe de fonctionnement repose sur les éléments suivants l'interaction du champ magnétique et le contrôle du courant.
Un moteur pas à pas se compose généralement de deux parties, un stator et un rotor.
Il y a plusieurs bobines sur le statorChaque bobine est appelée phase.
Il y a plusieurs pôles sur le rotorChaque pôle est également appelé phase.
Lorsque le courant passe à travers les bobines du stator, un champ magnétique est généré dans le stator, qui interagit avec les pôles magnétiques du rotor, entraînant la rotation de ce dernier.
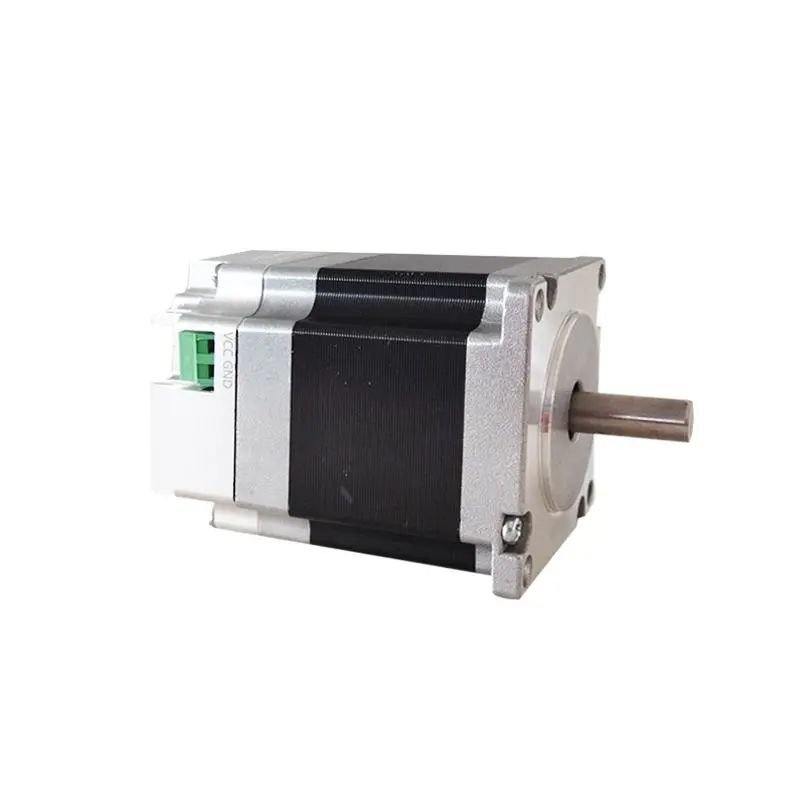
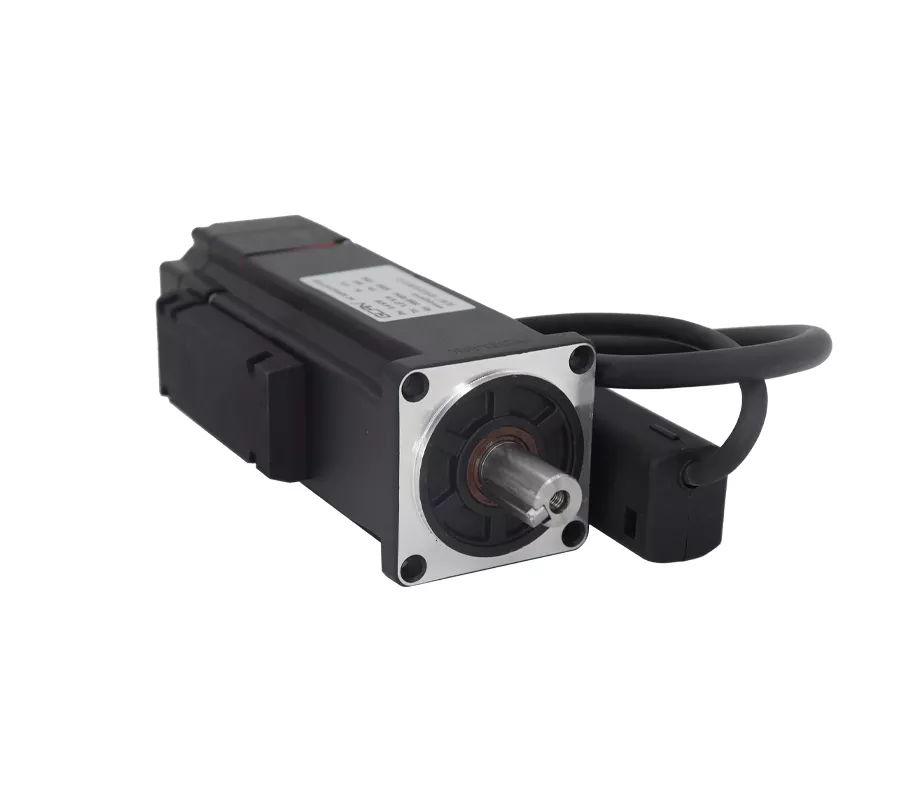
La rotation du moteur pas à pas s'effectue selon une certaine taille de pas.
Chaque fois qu'un signal d'impulsion électrique est reçu, il tourne d'un pas et le rotor tourne d'un angle fixe.
Par conséquent, les moteurs pas à pas peuvent contrôler très précisément l'angle et la vitesse de rotation.
Les différents types de moteurs pas à pas ont des principes de fonctionnement différents : monophasé, biphasé, triphasé. Cependant, leur principe de base est de utiliser le courant pour contrôler l'interaction des champs magnétiques afin d'obtenir un mouvement mécanique.
Les moteurs pas à pas biphasés sont les plus courants, avec un angle de pas de 1,8°, et le rotor tourne une fois chaque fois qu'il reçoit 200 impulsions.
À la recherche d'un Passerelle CAN Fibre Optique pour votre prochain projet ? Cliquez pour en savoir plus !