La actualización del PLC es un proceso complejo en el que intervienen muchos aspectos. Es necesario prestar atención a los siguientes puntos clave:
1.Precauciones para la actualización del hardware
Comprender las especificaciones actuales del hardware del PLC:
Antes de llevar a cabo una actualización de hardware, primero es necesario conocer a fondo el actual PLC las especificaciones de hardware, incluido el modelo de CPU, el tamaño de la memoria, el tipo de módulo de entrada y salida (E/S), etc. Esto ayuda a determinar qué componentes deben actualizarse.
Determine los requisitos de actualización:
En función de las necesidades reales de la línea de producción y de los planes de desarrollo futuros, determine los componentes de hardware que deben actualizarse. Por ejemplo, si la línea de producción funciona con lentitud, puede que necesite actualizar la CPU para aumentar la velocidad de cálculo; si necesita añadir nuevas funciones de control, puede que necesite añadir nuevos módulos de E/S o módulos de comunicación.
Elija los componentes de hardware adecuados:
Elija los componentes de hardware adecuados en función de los requisitos de actualización. A la hora de elegir, hay que tener en cuenta factores como los indicadores de rendimiento de los componentes, la compatibilidad y el coste. Asegúrese de que los nuevos componentes son compatibles con el sistema existente y pueden satisfacer las necesidades reales de la línea de producción.
Sigue la guía de instalación:
Instale y conecte los nuevos componentes de hardware de acuerdo con la guía de instalación proporcionada por el fabricante del PLC. Esto puede implicar operaciones como apagar, retirar el equipo antiguo e instalar el nuevo. Durante la operación, es necesario garantizar la seguridad y seguir las especificaciones pertinentes.
Medidas de seguridad:
Durante el proceso de instalación, asegúrese de tomar estrictas medidas de seguridad, como excluir del área de trabajo a todo el personal innecesario y asegurarse de que todas las fuentes de alimentación estén desconectadas. Cuando se utilicen los componentes internos, deben llevarse guantes antiestáticos para evitar descargas electrostáticas.
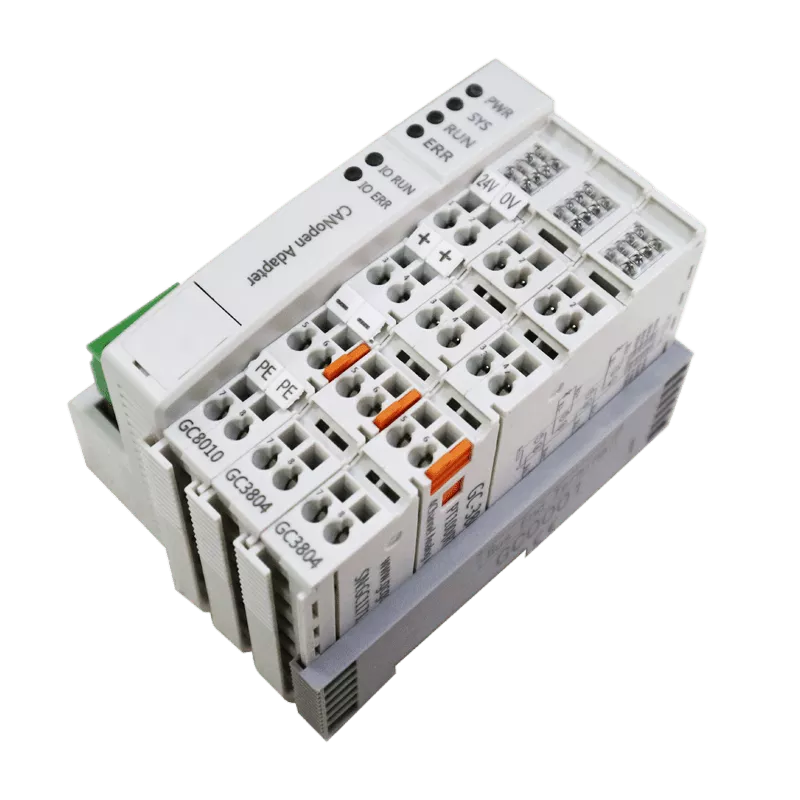

2.Precauciones de actualización del software
Haz una copia de seguridad del programa y los datos originales:
Antes de realizar una actualización de software, asegúrese de realizar una copia de seguridad del programa actual del PLC y de la configuración de los parámetros. Esto es para evitar la pérdida de datos o daños durante el proceso de actualización. El archivo de copia de seguridad debe guardarse en un lugar seguro para poder restaurarlo cuando sea necesario.
Descarga la nueva versión del programa:
Visite el sitio web oficial o la plataforma de soporte técnico del fabricante del PLC para descargar el nuevo archivo de firmware o software para el modelo y la versión del PLC. Asegúrese de que el firmware o software descargado es compatible con el sistema PLC.
Prepare el entorno de actualización:
Prepare las herramientas y el entorno de actualización necesarios, como software específico, controladores, interfaces de comunicación, etc. Configure el entorno de actualización de acuerdo con las directrices del fabricante del PLC.
Establece una conexión:
Conecte el ordenador al dispositivo PLC utilizando un cable de conexión o una interfaz de comunicación adecuados. En función del modelo de PLC y del método de conexión, es posible que necesite utilizar un puerto serie, Ethernet o una interfaz USB para conectarse.
Ejecute el software de actualización:
Abra la herramienta o software de actualización y siga las instrucciones de la interfaz. Normalmente, el software proporciona una interfaz gráfica para seleccionar los archivos de actualización, confirmar las opciones de actualización e iniciar el proceso de actualización.
Prueba y depuración:
Una vez finalizada la actualización, realice una prueba y depuración exhaustivas del sistema. Verifique el rendimiento y la estabilidad del nuevo sistema ejecutando tareas reales para asegurarse de que todas las funciones funcionan como se espera. Al mismo tiempo, compruebe si hay algún problema o error potencial y soluciónelo a tiempo.


3.Otras consideraciones
Comprobación de compatibilidad:
Cuando seleccione nuevos componentes de hardware o software de programación, asegúrese de realizar una comprobación de compatibilidad. Asegúrese de que los nuevos componentes o el software sean compatibles con el sistema existente para evitar situaciones en las que no puedan conectarse o no puedan utilizarse con normalidad.
Consulte a profesionales:
A la hora de tomar decisiones de actualización importantes, lo mejor es consultar a técnicos o ingenieros con amplia experiencia y conocimientos. Pueden asesorarle sobre la base de su experiencia práctica y sus conocimientos para ayudarle a tomar decisiones acertadas.
Aprendizaje continuo:
La tecnología PLC evoluciona y se actualiza constantemente, por lo que es muy importante seguir aprendiendo nuevos conocimientos y nuevas tecnologías. Mejore continuamente sus habilidades y conocimientos asistiendo a cursos de formación, leyendo libros profesionales y prestando atención a las tendencias del sector.
Si necesita un controlador PLC, no dude en ponerse en contacto con nosotros en 008613644001762/info@gcanbus.com