Probar y controlar un PLC es un proceso polifacético diseñado para verificar la funcionalidad, el rendimiento y la estabilidad de un sistema PLC. A continuación se explican brevemente los principales pasos y métodos de prueba y control de PLC.
1. Compruebe la alimentación y el estado de entrada/salida del PLC:
(1) Observe el estado de la indicación de alimentación, la indicación de error y la luz indicadora de entrada/salida del PLC para determinar si existe un problema de alimentación o una anomalía de entrada/salida.
(2) Compruebe si la conexión y la comunicación entre el PLC y los dispositivos externos son normales probando los puntos de E/S, incluidos los botones de funcionamiento, los botones de parada de emergencia, los indicadores de funcionamiento, los cilindros y sus finales de carrera, etc.
2. Utilice la función de diagnóstico del software:
(1) Muchos PLC llevan incorporados programas de diagnóstico que pueden detectar fallos de hardware y emitir información sobre los mismos. Accediendo al software de programación del PLC o utilizando herramientas de diagnóstico específicas, se puede leer y analizar la información de diagnóstico para determinar la causa específica del fallo.
(2) Comparar si el valor real coincide con el valor esperado para determinar si existe un punto de fallo.
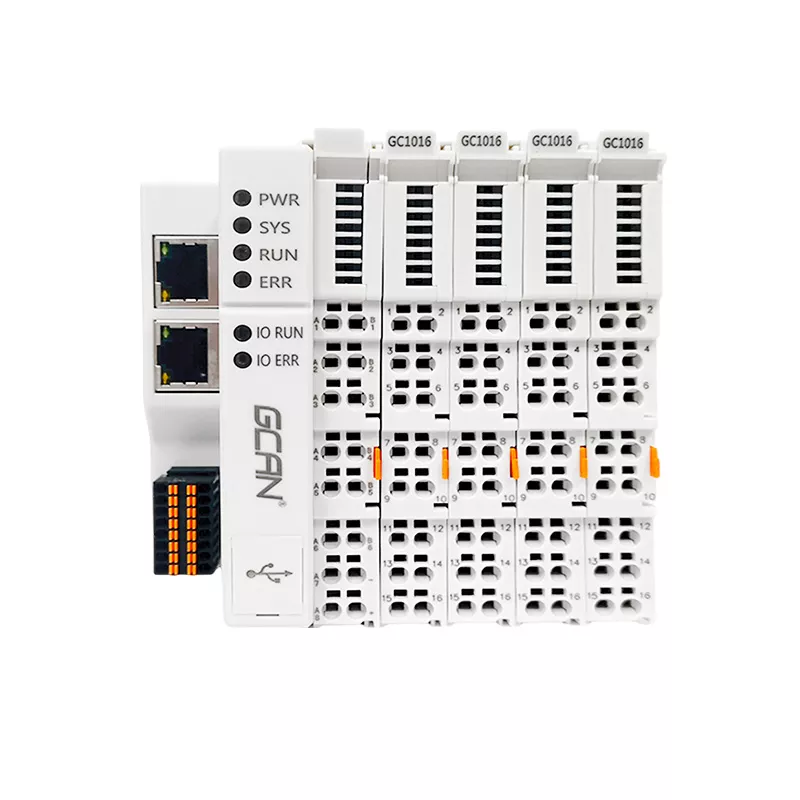
controlador logico programable plc fabricante chino precio low cost

3. Compruebe el programa lógico:
(1) Compruebe cuidadosamente PLC programa lógico para asegurarse de que las condiciones lógicas, temporizadores, contadores, etc. están ajustados correctamente y coinciden con el funcionamiento real del equipo.
(2) Compruebe la lógica de detección de fallos y alarmas en el programa lógico para determinar si existen posibles puntos de fallo.
4. Comprobación del estado de la comunicación:
(1) Si el PLC se comunica con otros dispositivos, como interfaces hombre-máquina (HMI), sensores o actuadores, compruebe la configuración del enlace de comunicación y del protocolo de comunicación.
(2) Utilizar la función de comunicación de red del PLC para el diagnóstico de fallos, utilizar herramientas de análisis de red para supervisar el proceso de comunicación y comprobar si la transmisión de paquetes de datos es normal.
5. Prueba de hardware:
(1) Utilizar herramientas de diagnóstico especializadas para la detección de fallos, como analizadores lógicos, osciloscopios y otros equipos de prueba de hardware.
(2) En el caso de sistemas grandes, debe establecerse una tabla de pruebas, es decir, marcarse después de las pruebas. Si se descubren errores de cableado durante el proceso de construcción, hay que solucionarlos de inmediato.
6. Compruebe la estructura mecánica y la carga del motor:
(1) Compruebe si la estructura mecánica está sujeta, etc., y si la carga del motor está debidamente protegida para evitar accidentes.
7. Depuración modo manual/modo semiautomático y relaciones lógicas relacionadas:
(1) Depurar el modo automático de acuerdo con el proceso de producción para asegurar que el PLC puede trabajar normalmente en diferentes modos.
8. Compruebe los archivos de registro y la información de alarma:
(1) Los sistemas PLC suelen registrar archivos de registro e información de alarmas, que pueden utilizarse para registrar eventos de fallo. Al ver estos archivos, puede determinar cuándo se produjo un fallo, su tipo y su ubicación.
9. Reinicio del hardware:
(1) En algunos casos, se puede utilizar el método de reinicio por hardware para resolver algunos problemas temporales.
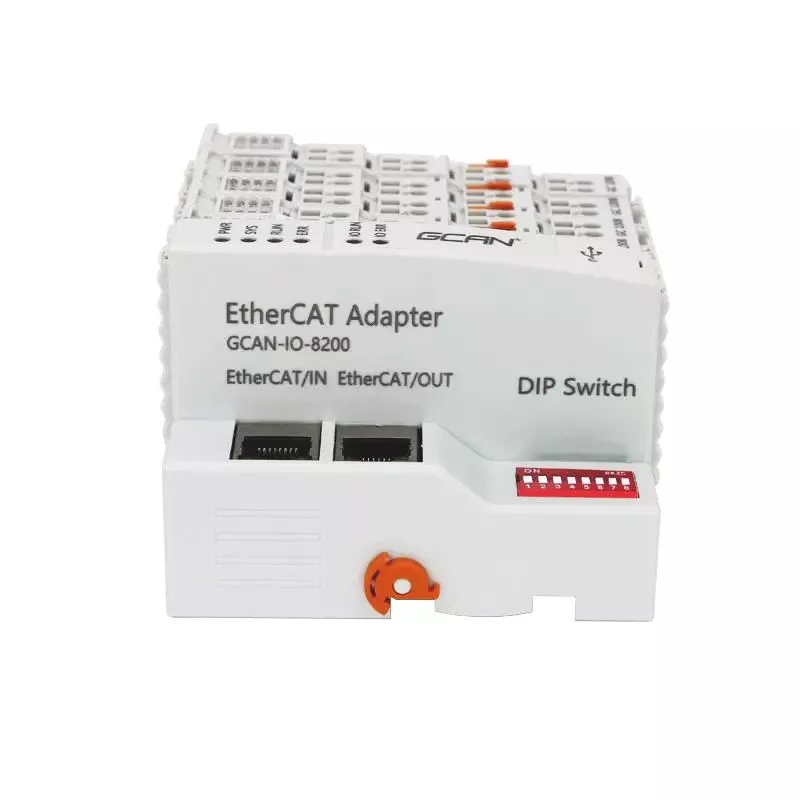
Si necesita un PLC compatible con la programación codesys, póngase en contacto con nosotros en 86 136 4400 1762 en cualquier momento.