1968년 PLC가 만들어지기 전까지 산업 공정은 일련의 유선 릴레이 뱅크, 타이머, 카운터로 처리되었습니다. 이러한 뱅크는 많은 공간이 필요하고 문제 해결에 많은 시간이 소요되었습니다. 릴레이에 문제가 생기면 전체 시스템이 고장날 수 있었습니다. PLC의 탄생으로 이러한 광범위한 시스템을 단일 모듈로 대체할 수 있게 되었습니다. 기술자는 래더 로직을 사용하여 이전에 릴레이와 타이머 뱅크에서 처리했던 것과 동일한 프로세스를 수행하도록 PLC를 쉽게 프로그래밍할 수 있었습니다. PLC는 정전 시에도 메모리를 유지하며 산업 공정에서 발생하는 먼지와 오염에 강했습니다.
PLC는 초창기 이후 천문학적인 발전을 거듭해 왔습니다. 그래픽 인터페이스부터 무선 연결, 머신 러닝에 이르기까지 오늘날의 PLC는 과거와는 비교할 수 없을 정도로 발전했습니다. 이제 고객은 애플리케이션의 요구 사항을 충족하는 맞춤형 PLC를 선택할 수 있습니다.
PLC를 선택할 때 고객이 애플리케이션에 적합한지 확인하기 위해 먼저 고려해야 할 몇 가지 사항이 있습니다.
가장 먼저 평가해야 할 요소는 애플리케이션에 필요한 입출력 장치의 수입니다. 얼마나 많은 아날로그 또는 디지털 입력과 출력이 필요한가요? PWM 출력이 필요한가요? I/O에 필요한 전압 및 전류 요구 사항은 무엇인가요?
고려해야 할 몇 가지 유형의 출력이 있습니다.
- 솔리드 스테이트는 트랜지스터 출력 PNP 또는 NPN을 사용하며 저전압 및 전류 제한이 적용됩니다.
- 릴레이 출력은 정상 개방(NO) 또는 정상 폐쇄(NC)로 표시됩니다. 일반적으로 쌍으로 연결되지만 여러 출력과 공통 접점을 공유할 수도 있습니다. 릴레이 출력은 PLC로부터 분리되어 있기 때문에 더 높은 전압과 전류를 허용합니다.
- PWM 또는 펄스 출력은 출력 레벨을 변경할 수 있어 모터와 같은 장치를 제어하는 데 유용합니다.
- 디지털 출력은 일정한 전압을 제공합니다. 로직 기반이며 릴레이 또는 표시기를 활성화하는 데 사용할 수 있습니다.
- 아날로그 출력은 일반적으로 해석을 위해 다양한 신호를 다른 장치로 보내는 데 사용됩니다. 아날로그 출력은 전압 또는 전류에 따라 분류되며, 일반적으로 1 - 5V, 0 - 10V, 0 - 20mA 또는 4 - 20mA로 구분됩니다.
인터페이스는 PLC의 또 다른 중요한 측면입니다. 현재 많은 PLC에는 터치스크린 또는 LCD와 푸시 버튼이 통합되어 있습니다. 이를 통해 PLC를 즉시 변경할 수 있는 기능을 제공합니다. 대부분의 PLC는 노트북이나 컴퓨터와 통신하지만, 이제는 태블릿이나 스마트폰과 같은 모바일 디바이스와도 연결할 수 있는 제품도 많습니다.
다음으로 고려해야 할 요소는 커뮤니케이션이며, 오늘날에는 다음과 같은 다양한 프로토콜을 사용할 수 있습니다. 컴포버스, 디바이스넷, 이더넷/IP, 이더캣, RS-232C, RS-422, RS-485. 이더넷/IP 및 EtherCAT 은 앞서 언급한 프로토콜 중 인터넷 기능을 갖춘 유일한 두 프로토콜이기 때문에 매우 널리 사용되고 있습니다. 이더넷/IP의 잠재적 데이터 전송 속도는 1Gbps이며, EtherCAT은 100Mbps입니다. 두 프로토콜 모두 최대 케이블 길이가 100미터입니다. IIoT가 시작되면서 무선 통신을 제공하는 많은 PLC도 시장에 출시되고 있습니다. 셀룰러 통신을 통해 안전한 클라우드로 정보를 무선으로 업데이트할 수 있는 기능을 갖춘 PLC를 더 이상 드물지 않게 찾아볼 수 있습니다.
프로그래밍은 평가해야 할 또 다른 측면입니다. 프로그래밍 소프트웨어는 제조업체마다 다릅니다. 일부 제조업체는 무료 다운로드를 제공하는 반면, 다른 소프트웨어는 별도로 구매해야 하거나 구독이 필요합니다. 소프트웨어는 일반적으로 PLC에 고유합니다. 소프트웨어 패키지를 살펴보면 필요한 프로그래밍 언어에 대한 아이디어를 얻을 수 있으며, 이는 한 언어에 더 익숙하고 다른 언어에 덜 익숙할 수 있으므로 유용합니다.
대부분의 PLC에는 전원 공급 장치가 장착되어 있지 않으므로 PLC를 선택한 후에는 전원 요구 사항을 검토해야 합니다. PLC에 24VDC가 필요한지 110VAC가 필요한지 여부에 따라 필요한 요구 사항을 충족하는 별도의 전원 공급 장치를 찾아야 합니다.
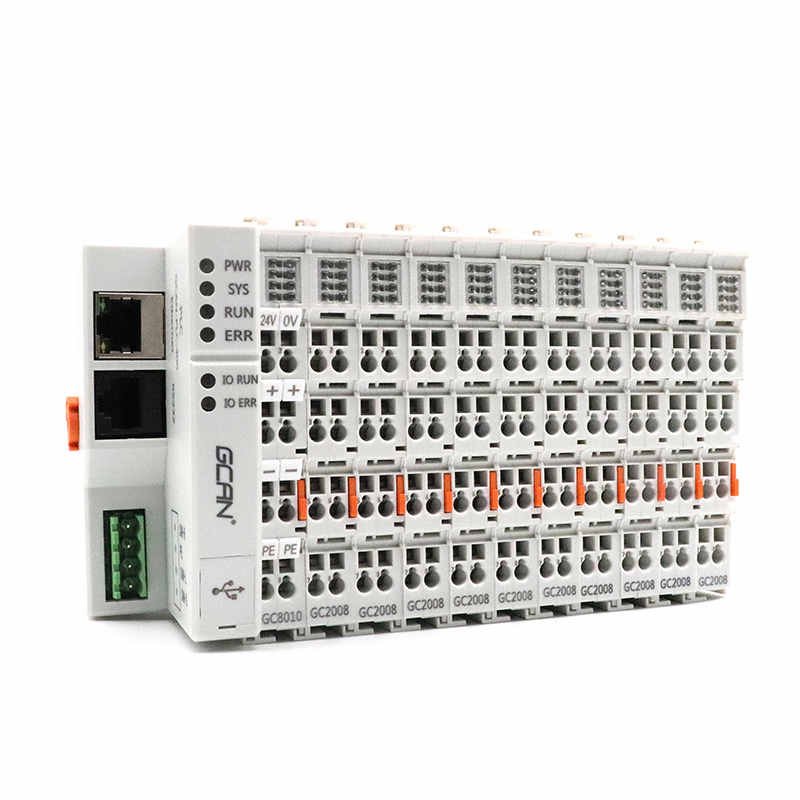
찾고 계십니까? PLC I/O 커플러? 자세히 알아보려면 클릭하세요!